This content was published: August 6, 2010. Phone numbers, email addresses, and other information may have changed.
PCC training programs are getting people to work
Photos and story by James Hill
In a tough employment environment, there is hope for local job-seekers and for companies that need qualified employees.
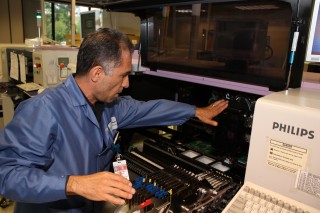
Iranian Seifollah Mojab was laid off twice before finding a steady job with Beaverton’s Vanguard EMS via PCC’s Entry Level High tech Training Program.
For past nine years, Portland Community College’s Washington County Workforce Development Center has offered a free, seven-week training program that helps people gain employment in the high-tech sector. The Entry Level High Tech Skills Training Program has seen 90 percent of its students find a job with the program’s consortium of high-tech employers like Vanguard-EMS, Precision Wire Components, Axiom Electronics and ViaSystems (formally Merix Corp.) This program is financed in whole or in part with funds provided through Worksystems Inc., via the U.S. Department of Labor.
In addition, PCC runs the Manufacturing Foundations Program, a six-week class that trains students in the basics of working in manufacturing. College staff work with area employers, including ViaSystems, Clear Edge Power, TOK America and Precision Wire Components, who select the students for the class and then interview them for positions at the end of the training. Also, PCC works directly with WorkSource Oregon (Employment Department) to help unemployed workers get back to work through these two training programs. It funds regular short-term training through PCC academic programs like solar, bioscience and renewable energy to help people become more employable.
Program grooms future employees for companies
The Entry Level High Tech Skills Program gives students the opportunity to tour local high tech companies, gain math skills for manufacturing work, learn communication and teamwork skills, explore quality systems like lean manufacturing, get instruction on basic hand tools such as calipers and micrometers, work in component identification, and gain 20-hours of soldering.
Iranian Seifollah Mojab, 50, spent 12 years trying to immigrate to the United States. Three years ago, he was finally able to move his family to Oregon to escape the political turmoil of his home country. But he needed to find a job to support his family so he turned to PCC. Mojab had been laid off from his first job here after just three months at a local plant manufacturing parts for Toyota cars. After taking the placement test, he spotted a flyer advertising the program. In 2008, he was accepted after passing all of the requirements for the training.
Read more about how Mojab found opportunity through PCC’s training partnership.
“It was very good training,” Mojab said. “This training helped me a lot to get familiar working in the U.S. especially in high tech field. I learned not only about the training, but also the industry and how to improve my skills in communications and how to help my family.”
Due to the poor economic conditions, Vanguard went through a round of layoffs and Mojab lost his job. He was hired back a month later and received additional support from the company, eventually getting promoted to surface mount technology operator. This couldn’t have happened if Mojab hadn’t had the initial entry-level training at PCC.
“Every day I learned more and more,” he said. “It’s a very nice place here. (My entry-level training) affected my whole life. I’m too lucky to have seen that poster. If I didn’t see it I don’t know where I’d be right now.”
Industry grateful for PCC training
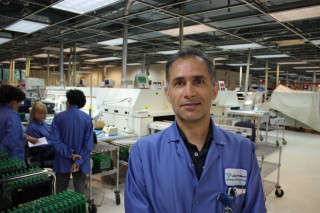
‘This training helped me a lot to get familiar working in the U.S., especially in high tech field,’ said Mojab.
For the partner companies, the program gives them an opportunity to pre-screen employees like Mojab before hiring them. Trish Hennon, director of human resource for Precision Wire Components in Tualatin, said the training program has been invaluable in providing a pool of qualified workers.
“We’ve been involved in the plan since it started,” Hennon said. “We’ve probably hired 25 workers out this program and they tend to stick. We have had good success and the graduates have the foundation skills to succeed. When they come to us off the street there is a learning curve. The training we give and supplemental training has been nicely backfilled by this program so they are up to speed and they get it.
“It’s been fabulous,” she added. “The people who facilitate the program really take care of us. They know what our needs are. It’s been very good process.”
In 2002, the Entry Level High Tech Skills training was started by ViaSystems, an electronics manufacturer in Forest Grove. Other electronics firms joined later (Benchmark, Vanguard EMS and Matsushita) and formed a consortium through which they provided input on curriculum and interviewed and selected students for the training.
ViaSystems provided the original seed money and PCC Capital Career Center developed the curriculum for the seven-week training program and provided instructors. As a result, 87 percent have been hired into full time employment with these companies, which is more than 220 in total.
“Our goal is to provide a continuous supply of qualified workers from the local community for companies,” said Linda Browning, business services coordinator for PCC. “Employers actively participate and have a stake in the outcome by selecting students for the classes, helping update the curriculum, offering company tours and presentations, and hiring from the pool of graduates each term.”
At Vanguard EMS in Beaverton, Tesa Patton, the company’s director of human resource, said it joined the partnership during a spell of layoffs. Knowing that the layoffs wouldn’t last, Vanguard felt it was a good way to expand their pool of qualified candidates once the job market recovered, she said.
“We plan each years recruiting program around the classes and try to hire as many of the graduates as possible,” Patton said. “This has brought a tremendous amount of talent into our organization.”
Training builds available pool of workers
Patton and her company have hired more than 30 people from the program and there are currently 11 former PCC students in the company. She said the key has been that the skills training doesn’t just train people to do entry-level work.
“It has given them knowledge, skills and stoked passion for what we do so that they have the potential to move and grow within the company,” Patton said. “Our managers are always excited to be in a position to hire these graduates. They say training them is significantly easier than training new hires from outside the program.”
Even though the economy is still in the doldrums with the state unemployment rate hovering above 10 percent, demand for qualified manufacturing workers hasn’t dwindled. All of the companies involved need workers because the pool has evaporated year after year.
“The economy continues to go up and down and is worse now than it has been in all the years we have been involved, but the labor pool for electronics manufacturing continues to dwindle,” Patton added. “High schools are not producing graduates who have any knowledge that this kind of manufacturing exists. Colleges openly discourage their students from pursuing manufacturing as the perception is that it has all gone off shore or soon will be. While this is certainly a pervasive trend, many companies like ours have found the niche of what to manufacture in the U.S. and struggle to find quality, interested candidates.”