This content was published: September 19, 2016. Phone numbers, email addresses, and other information may have changed.
PCC secures $577,500 to develop advanced manufacturing talent
Photos and story by James Hill
Portland Community College is on the lookout for great manufacturing talent.
PCC received a $577,500, one-year grant from the Oregon Talent Council for the Realizing Advanced Manufacturing Potential in Portland (RAMP PDX) Project. RAMP PDX will train, place, advance and retain participants in a variety of advanced manufacturing jobs. The project will increase the skilled worker pipeline for the many advanced manufacturing companies in the region and pave the way for workers to attain certificates and degrees. Plus, the college will contribute $1.5 million to the RAMP PDX’s efforts.
The partnership is an example of PCC transforming the community by creating opportunity. The college promotes economic and community development through community engagement and workforce development programs that are responsive to community and business needs.
“PCC has a successful track record of working in collaboration with industry to design and develop training and education programs that are responsive to emerging needs,” said Marc Goldberg, the college’s associate vice president of Workforce Development and Community Education.
“Advanced manufacturing jobs present good opportunities for unemployed, incumbent, career changers and under-skilled individuals,” he added. “This project aims to draw participants who may have never considered advanced manufacturing as a career option, or are looking for advancement opportunities within the industry. The grant will help PCC increase the pipeline of workers for the many advanced manufacturing companies in the region.”
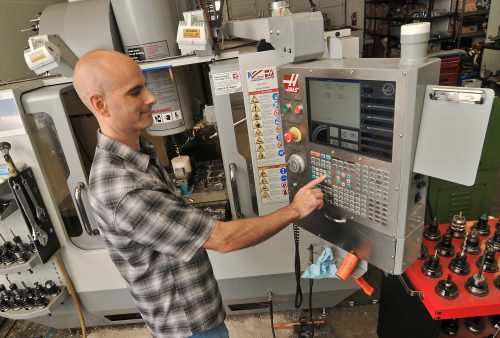
PCC will partner with four companies, which include Festo Didactic Inc., Leupold + Stevens, Inc., RapidMade and Rose Technical Graphics, to serve about 300 participants in the RAMP PDX Project.
PCC will partner with four companies, which include Festo Didactic Inc., Leupold + Stevens, Inc., RapidMade and Rose Technical Graphics, to serve about 300 participants in the RAMP PDX Project. Coordinators will organize outreach events at PCC’s MakerSpace Lab to introduce advanced manufacturing training, career and educational options in the industry to new audiences.
A Computer Aided Design and Drafting (CADD) short-term certificate and non-credit Mechatronics Technology Program will be created. These will assist incumbent workers with “skilling-up” and connect them to more advanced mechatronics training and other education opportunities, respectively. These activities will help RAMP PDX target the technologically skilled mechanics, maintenance technicians, industrial machinists, millwrights, operators, machinery maintenance technicians, industrial machinery mechanics and machinists occupations.
This investment in PCC is one of five recent grant awards [pdf] by the Oregon Talent Council to support statewide projects that provide students and existing workers with skills to increase their employability in Oregon’s high demand occupations.
“These grants will support the upgrading and retooling of skills for Oregon’s existing and future workers,” said David Childers, chair of the Talent Council. “It is critically important that we invest in the projects that keep skills fresh in the face of new technology and build new models for education and training that keep pace with changing business needs.”
The Talent Council was created by the 2015 Oregon Legislature with a fund of $6.1 million to seed investments in talent development programs. The Talent Council works with industry, workforce organizations and the Oregon higher education community to help fill high wage, high demand occupations in the state.
“With these awards, the Talent Council continues to provide leadership and raise awareness about the importance of talent to our economy and communities,” said Kay Erickson, director of the Oregon Employment Department. “These grants support delivery of training and education in critical occupations to Oregonians, regardless of where they live or work, and underscore the powerful partnership of education and industry in meeting talent and workforce needs.”
For more information, visit www.oregontalentcouncil.org.

Is there some sort of orientation for this program? If so, what day and time? If not, where can I get more information? What is the cost to the student…?
Thanks!
This looks like a great opportunity for many people. I have been looking for work for 6 years and going to school at MHCC and now PCC. Will complete Administrative Assistant Associate degree in March 2017. I am interested in a career in Medical Information Management or Medical Record Management. I wish there would have been a program that focused on medical office procedures. It’s hard to get a job in the healthcare industry without any experience. Hopefully I can find a job soon. The patient access program at the CLIMB center looks good but I don’t have the money to take the classes. If it’s an entry level program, how is somebody going to have the money to advance in their profession when they don’t have one? Confusing.
You can always contact Workforce Development to see when the project will begin. http://www.pcc.edu/resources/careers/workforce/
While this seems like a good idea at first glance from an industry perspective, how does PCC intend to get students to this “level”, especially considering quality equipment is priced in the millions of dollars? (excluding the yearly salary of someone who can both operate and teach both the equipment and class(es), which I imagine to be about equal to the amount you have annotated in cash plus benefits, retirement, etc.)
Machining and manufacturing is an art, not just a technical skill. Understanding trigonometry, unit circles, and polynomial equations are just a small part of the required skill set. One learns how to run a lathe first (after spending two years watching and sweeping up the vicinity), because then one understands innately (and more intimately) the job and methods involved in programming or debugging more dynamic equipment — such as a CNC, water-jet, laser-mill, or largescale 3D printer. Conversely one is not simultaneously constricted by technology, but still able to break out the drill press and cut gears the old-fashioned way — when required.
Also, I think producing a vast amount of workers that can “program” a CNC or similar from instructions, is ultimately unfair to both the student and community. We already get such labor from temporary agencies and technical schools, neither of which has been successful in reinventing or revitalizing the United States manufacturing industry. Those that have been successful outside of large corporations and conglomerates, have been individuals with the knowledge and initiative to create an original product with an original design — one that is created with care and craftsmanship which is learned through time, trial, and error. This is an entirely different and separate construct from the mostly antiquated style utilized at PCC — to the best of my knowledge.
Perhaps I myself am the antiquated one — but I believe firmly that sweeping the floor, cleaning the tools, watching before doing, planing before proceeding, building one’s toolbox by hand, and knowing the history is far more important than the required math. One comes to the understanding of tooling and it’s calibration through breaking tooling and producing bad parts, these data are placed inside one’s “memory_box”; which keeps you safe and informs your future actions; this is not something you can learn from a book but is rather something that comes from working with a master in the craft and drowning oneself in the environment and methods.
As such, it requires me to annotate, nontraditional students can’t practically afford internships (traditionally). This is the actual limiting factor to their success. As such, this is the service the college should provide. Investing in students to work on and design real products, making real mistakes they can learn from, in the ‘real world’. The more traditional lecture or technical school model doesn’t work, not in a world where one is required to hit the ground running on day one.
What I hear in this article are aspirations and generalizations — what I don’t hear is real and detailed plans which provide a road map for these platitudes to be actualized.
I believe that PCC offers the basics of education for manufacturing. To introduce concepts, methods and a working knowledge of math and design. Manufacturing like many other professions, requires hands on experience. PCC could incorporate a work study program with a number of local manufacturing facilities in various industries to start the student out into a “real world” experience. This would be invaluable as many times an employer will HIRE a person after an internship rather than retrain a new hire.
[…] collaboration with the college is creating a pipeline of trained workers for the manufacturing […]